Charcoal machine equipment is the main equipment for the professional production of machine-made charcoal. In this equipment, it has many components, and the propeller is a vulnerable part of the charcoal machine equipment. Users need to pay more attention to the operation problem and repair it monthly to ensure its Production efficiency and effectiveness, so what should I do if the propeller of the charcoal machine is worn? How to maintain the propeller of the charcoal machine?
Operating skills of charcoal machine
- After the machine-made charcoal machine works for a long time, the motor pulley must be repaired, whether to add oil, whether to clean up the dirt, so as to improve the service life of the machine.
- Sometimes the machine-made charcoal machine will loosen the belt after working for a long time, then the speed of the machine will be reduced a lot. This is the reason why the output of the long-term work cannot be increased, so it is necessary to check the tightness of the belt.
- Check whether there is a large load in the operation of the motor. Long-term damage to the motor will affect the working efficiency of the whole machine. The combustible gas produced by the combustion of the combustibles of the charcoal machine equipment in the pipeline is sprayed, cooled, purified, etc.
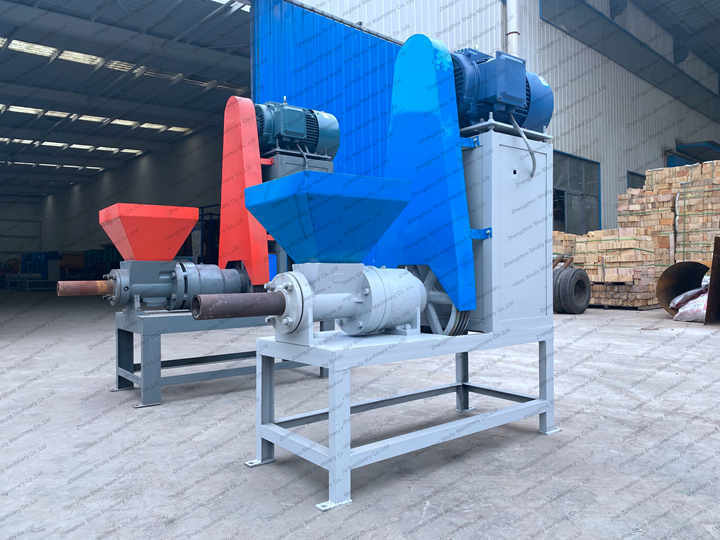
How to maintain the propeller of the charcoal machine?
What should I do about the wear of the propeller of the charcoal machine? The wear of the propeller in the production process of the charcoal machine is very fast.
To solve this problem is actually very simple. First of all, the raw materials must be ensured to be dry, so that the wear of the propeller is relatively small, and the particle size and impurity content of the saw have an impact on the degree of wear, and the size of the motor is too small. Since the power is not small enough, the horse-drawn cart will also cause the acceleration of the thruster wear. It is better to choose high-carbon steel wear-resistant electrode when welding the thruster.
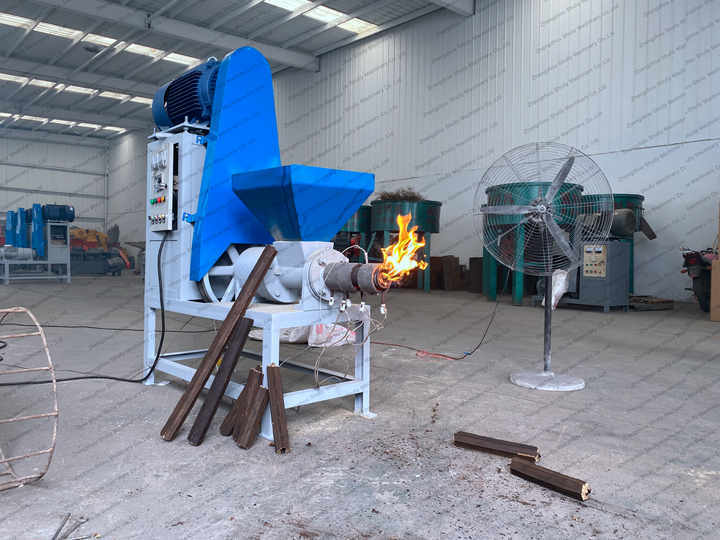
Tips in the use of the sawdust briquette machine
- Check the oil level of the machine before starting the machine. Generally, add about 750ml of oil for lubrication and machine maintenance.
- Before use, start and run without load for ten minutes to check whether there is jamming or blockage. If an abnormality is found, the machine needs to be shut down immediately to find the cause. After the fault is removed, check the operation buttons of the corresponding equipment during operation. The green button (forward rotation), the red button (stop), and the yellow button (reverse).
- The preset temperature needs to be adjusted before feeding. Depending on the material, the boot temperature is generally between 260-380°C. Generally speaking, miscellaneous wood sawdust can be set to about 320°C, and the preset temperature of rice husk is about 260°C. Other materials are adjusted according to the hardness of the material. The harder the material is, the corresponding temperature will increase by about 10℃.
- If the rod is produced too quickly or the color of the rod is black, it means the preset temperature is too high. At this time, you need to adjust the temperature control table, lower the temperature control table by 3℃ each time, and then continue to observe the situation until the color of the rod is brown. But the temperature of the rod-making machine should not be too low. If it is too low, it will cause too much resistance to fail.
- If there is a jam or the speed of the rod is too slow, and the color of the rod is too light, it means that the temperature is too low. Raise the high-temperature control meter to 5℃ each time until the rod is normal.
- When the machine is stopped, the remaining material in the hopper should be basically discharged, and then press the reverse button to make the material in the propulsion shaft withdraw. After shutting down, the heating ring needs to continue to work for 10 minutes to allow the remaining rods in the heating cylinder to become charcoal so that it can be used next time.