The charcoal briquette making machine is specially used to press coal dust or charcoal dust into various shapes of high-density coal or charcoal sticks. This equipment can not only make full use of the waste resources such as broken coal and coal dust, improve the utilization rate and calorific value of fuel, but also significantly reduce the production cost and create considerable economic benefits.
The shaped charcoal briquette is dense and resistant to burning, smokeless and odorless, and is widely used in many fields such as barbecue, boiler heating, energy production, agriculture, and industry, etc. It is an ideal choice for coal resource reuse and environmental protection, and energy saving.
Charcoal briquette making machine advantages
- It supports a variety of mold styles such as plum blossom shape, triangle, quadrilateral, rhombus, etc., which can be customized according to customers’ needs to meet different purposes.
- The pressed coal bar has high denseness, high strength and beautiful appearance, which is easy to store, transport and use.
- The whole machine runs with low noise and less abrasion, which guarantees the efficient production for a long time.
- The main charcoal briquette making machine is made of high-quality steel, with sturdy structure and prolonged service life.
- The core components such as the screw propeller (auger) are made of alloy material, which is wear-resistant and durable, reducing the frequency of replacement and lowering the maintenance cost.
Main structure of charcoal briquette extruder
The main structure of the charcoal briquette making machine is composed of a motor, a reducer, a screw propeller shaft, a mold, and the final cutter.
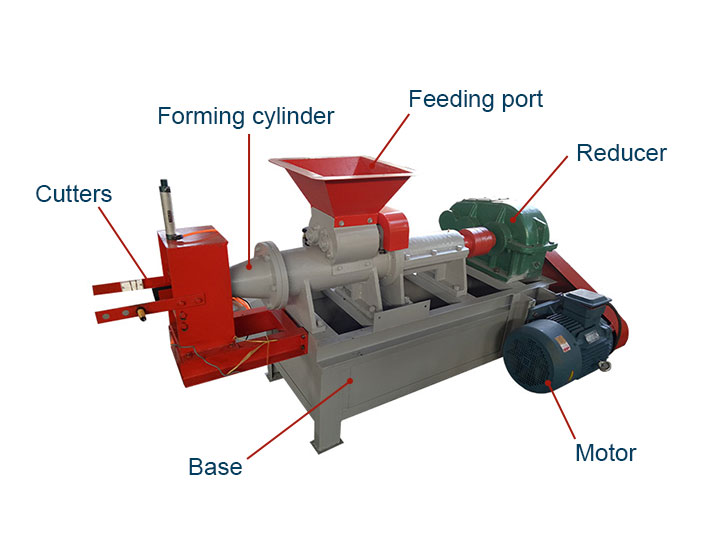
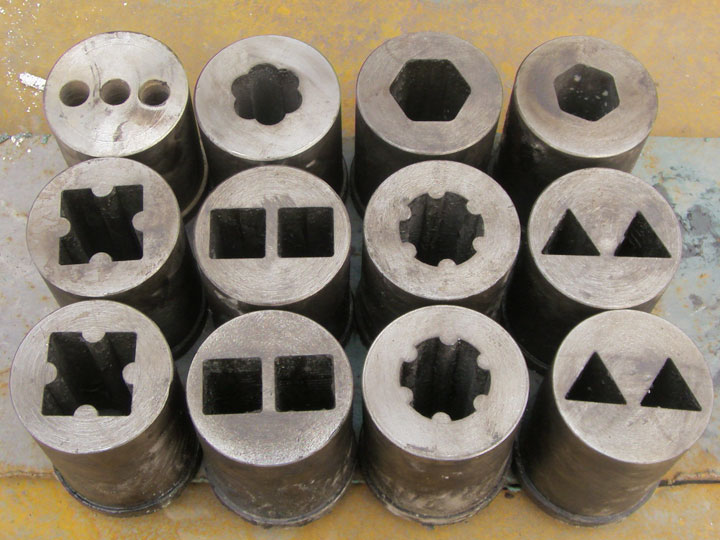
We provide a large number of different molds to choose from, and we can also customize them according to customer needs.
Working principle of charcoal briquette machine
The charcoal briquette making machine adopts a new screw extrusion principle to squeeze the prepared pulverized coal into a certain strength and predetermined shape of coal sticks.
- Our charcoal briquette making machine adopts the hard-tooth surface reducer, which is small in size and high in load capacity.
- The impeller inside the charcoal briquette extruder is designed with thickened blades, and the impeller and the inner liner of the cylinder are made of wear-resistant precision casting materials.
After the materials enter from the feeding port, they will be squeezed forward through the inner cone mold to make the compression between the materials extremely tight. There is strong friction between the material and the cylinder, which causes the temperature of the coal powder to rise while generating heat, the moisture and the binder are more uniform, the plasticity of the coal is also greatly increased, and finally, it is extruded in the flat part of the mold.
Three different cutting methods
- Pneumatic cutting device
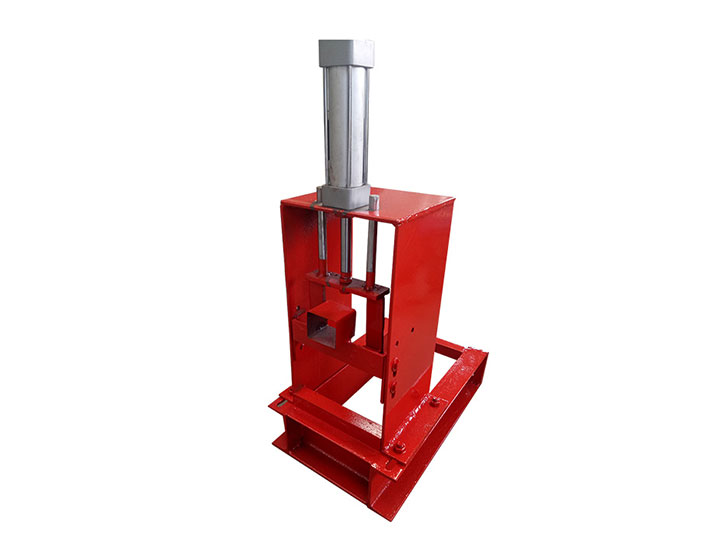
This kind of pneumatic cutting machine is generally equipped at the exit of the charcoal briquette making machine and equipped with an induction device. When the coal rod reaches a certain length, it will automatically cut.
2. Cubic charcoal cutting machine
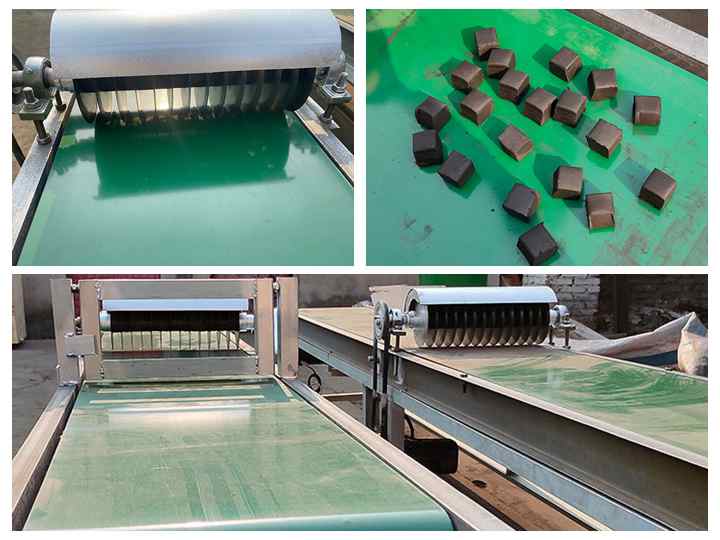
This cubic-cutting device is used to cut cubic coal. The cut coal rods pass through this machine to become coal blocks of uniform shape and size.
3. CNC cutting device
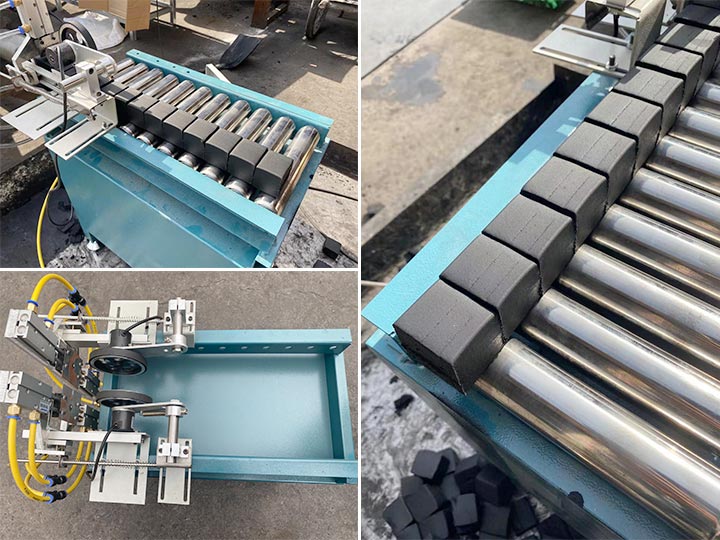
This is our latest coal-cutting machine. It adopts an intelligent control system, the cutting length of coal rods can be adjusted freely and can be used to cut coal rods of various shapes.
Display of charcoal briquette making machine
Coal briquette making machine technical parameters
Model | Power(kw) | Capacity(kg/h) | Weight(kg) | Dimension(mm) |
SL-140 | 11 | 500-600 | 850 | 2050*900*1250 |
SL-180 | 22 | 1000 | 1300 | 2500*1050*1100 |
Solutions to poor coal briquettes forming
- Adding binder: adequate amount of special binder can enhance the adhesion between the coal powder and improve the molding effect. It is recommended to choose the right type according to the characteristics of the coal powder, and do a small trial experiment to verify the effect.
- Improve the physical state of coal powder: crush the large particles of coal powder, and sieve out the gangue and other impurities, so that the particle size is smaller and the particles are uniform, which helps to improve the adsorption force between the particles and improve the molding quality.
- Control of moisture content: maintaining a suitable moisture content is the key to molding. Too low moisture content will lead to poor bonding, too high will affect the pressing effect. Depending on the situation, you can add water or use drying equipment for dehydration.
Tips for using charcoal briquette machine
- Idle check: before starting this charcoal briquette making machine, it should be idle to check whether the nut is loose, whether there is any foreign matter or abnormal sound, and to confirm that all parts are running normally.
- Lubrication and maintenance: before testing the charcoal briquette making machine, the key parts should be filled with an appropriate amount of lubricant to maintain smooth operation and prevent wear and tear.
- Daily inspection before starting the machine: make sure the machine is sensitive, no abnormal sound and idle for 2-3 seconds before putting it into use.
- Current monitoring to prevent overload: install DC voltmeter and ammeter to adjust the feeding quantity and material humidity according to the readings in time to prevent the equipment from being overloaded.
- Material pre-treatment: the particle size of raw materials must be less than 2mm, add the appropriate amount of water, binder and curing agent, mix well, and leave it for 24 hours before use.
- Discharge port cleanup: blocked only with a wooden stick or bamboo stick dredging, prohibited the use of metal tools, so as not to damage the equipment.
- Bearing maintenance: regularly add lubricating oil, keep the bearing temperature not more than 60 ℃, to extend the service life of the machine.
- Shutdown cleaning: empty the material in the barrel before shutting down the machine, then disassemble and clean the machine head, reassemble and prepare for the next production.
Feel free to contact us at any time
Thank you for your interest in our advanced charcoal briquette making machine technology! If you are interested in our coal briquette extruder machine or have any questions, please feel free to contact our professional team.
For more coal powder moulding machines, please check Coal Ball Briquette Machine | BBQ Coal Press Machine and Hydraulic&Mechanical Hookah Charcoal Briquetting Machine. We are willing to share more detailed information, customized solutions, and provide you with professional technical support. We look forward to establishing a cooperative relationship with you and jointly promoting the development of the industry!