Shuliy continuous carbonization furnace equipment production process model. The continuous carbonization furnace is very important to the wood carbon industry because the continuous carbonization furnace not only has a higher output than the cavern charcoal, but the most important one is the environmental protection problem. Under the influence of the environmental protection policy, the pollution gas generated by the charcoal burning cannot be treated. Therefore, charcoal burning charcoal cannot work properly.
The continuous carbonization furnace not only solves this problem, but also turns the problem into a flammable gas by means of research and development, and uses the gas itself to burn the heat it needs so that the gas is not discharged. And make full use of it, reducing the cost of carbides, which is what the wood carbon industry bosses are willing to see.
The workflow of the carbonization furnace is actually a circular process model. At first, the flue gas is generated by a gasifier (also known as a gas generator), and the flue gas generated at this time is a mixed gas with various impurities. The generated flue gas is then sent to a cyclone to remove dust from the gas. This is the first step in the production process.
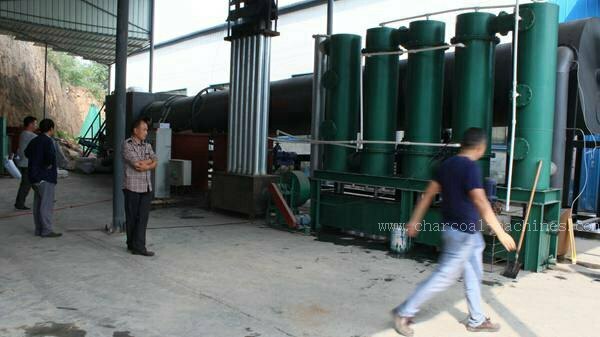
The gas is then further purified and ignited into an ignition device to provide heat to the host. When the host reaches the carbonizable temperature, it begins to carbonize the raw materials into the main unit.
Many people think that it is over here, and it is wrong. In the process of producing carbides, a lot of smoke will appear, and there will be more gas than the gasifier. At this time, we can cut off. The gas in the gasifier is then introduced into the purification system for purification and finally introduced into the ignition device that provides the host’s own temperature to form a closed loop production. It not only protects the environment but also saves energy.
Its output is very large, not as awkward as burning charcoal in the cave, continuous production under high-temperature conditions, generally 20 tons a day is also a normal thing, not as uncontrollable as burning charcoal in the cave, charcoal burning a raw material In the case of no change, if the change is made, the produced carbide is also unstable. It can do a variety of raw material carbonization, different raw materials with different temperature segments to charcoal. Solved the diversification of carbides in the market.